LABORATORY INSTALLATION FOR ZINC SULFIDIZATION BY CVD METHOD
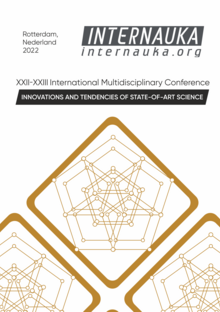
LABORATORY INSTALLATION FOR ZINC SULFIDIZATION BY CVD METHOD
Liza Dudaeva
Master, Higher School of Physics and Materials Technology Peter the Great Saint Petersburg University,
Russia, Saint Petersburg
Alexandr Semencha
Director, Higher School of Physics and Materials Technology Associate Professor, Department of Applied Chemistry Peter the Great Saint Petersburg University,
Russia, Saint Petersburg
ABSTRACT
The paper considers a CVD laboratory installation for zink sulfide production technology for further study in the field of IR detectors, amplifiers, phosphors and lasers.
Keywords: CVD, laboratory installation, vacuum installation, zinc sulfidization, zinc deposition, PWD, ZnS, Zn, Er.
The scope of application of ZnS is quite large: amplifiers and ultrasound detectors, infrared sensors, lasers, phosphors, solar cells, LEDs, photochemical cells, infrared detectors, catalysts, resistance switches and non-volatile memory devices.[1-3]
The two-stage technology for the production of erbium and zinc sulfides was developed thanks to a designed and assembled laboratory installation.
The cycle consisted of two steps:
1. Magnetron sputtering of a thin metal film (100-600 nm)
2. Sulfidization in a CVD two-zone reactor at reduced pressure. As a result, ErS and ZnS thin films were obtained at temperatures of 450 and 350 0C, respectively, in the argon carrier gas flow at a speed of 2 l/min. The temperature of sulfur evaporation was in the range of 160-190 0C.
Zinc deposition was carried out by magnetron deposition on an experimental installation in Fig.1.
Figure 1. Laboratory magnetron installation
The ZnS production plant is indicated in the form of a 3D model in Fig.2.1. and photos in the laboratory in Fig. 2.2.
The flanges in Fig. 4 and 5 were designed specifically for it, the complete technological scheme of the installation is shown in Fig. 3.
Figure 2.1. 3D Model of the CVD system
Figure 2.2. Laboratory installation of CVD for obtaining ZnS
Figure 3. Technological scheme of production
1 – Pre–vacuum pump, 2 – gas mixer, 3 – pressure gauge, 4 – furnace, 5 – quartz reactor, 6 – SOM, 7 - boats with evaporable material, 8 – balloon reduction gearboxes, 9 – RRG.
Figure 4. 3D model of flanges for CVD installation for obtaining ZnS
Figure 5. Flanges: a) output vacuum installation, b) intermediate vacuum installation, c) input vacuum installation
2. Conditions for obtaining nanocrystalline films of sulfide and erbium.
The spraying was tested using the example of erbium sulfide. In the future, the production of zinc sulfide occurred according to similar parameters.
First of all, the temperature distribution of the main furnace was checked.
The temperatures were recorded after continuous operation of the unit in full configuration for 1 hour at a temperature of 750 °C.
The graph of the temperature distribution inside the furnace, covering the quartz tube located inside the furnace distance, is shown in Figure 6.
Figure 6. Temperature graph of temperature distribution
Measurements were made using a thermocouple with a shift of 5 mm, the average heating time of the thermocouple after changing the position along the length of the reactor was 10 minutes.
Table 1.
A graph of the removal of temperature indicators from samples
№ |
T(min) |
T(°C) |
||
1 |
18.10 |
471.2 |
||
2 |
18.55 |
499.5 |
||
3 |
19.05 |
518.0 |
||
4 |
19.25 |
532.7 |
||
5 |
19.39 |
548.6 |
||
6 |
19.48 |
564.3 |
||
7 |
19.58 |
575.2 |
||
8 |
20.08 |
586.3 |
||
9 |
20.18 |
596.1 |
||
10 |
20.28 |
603.9 |
||
11 |
20.38 |
610.8 |
||
12 |
20.55 |
617.6 |
||
13 |
21.05 |
623.5 |
||
14 |
21.15 |
629.1 |
||
15 |
21.25 |
633.6 |
||
16 |
21.28 |
636.6 |
||
17 |
21.33 |
639.9 |
||
18 |
21.38 |
642.4 |
||
19 |
21.43 |
644.6 |
||
20 |
21.48 |
645.6 |
||
21 |
21.53 |
646.3 |
||
22 |
21.58 |
647.4 |
||
23 |
22.05 |
649.2 |
||
The temperature distribution from the center of the reactor is absolutely mirrored, therefore, further №. 23, the temperature decreased exactly according to the ascending principle indicated in Table 1. Thus, taking into account the theoretical review of the behavior of ZnS in the reactor [4-6], suitable temperature control points were identified for the location of samples during spraying.
That is, the schematic arrangement of the samples was located closer to the center of the reactor, compliance with this condition can be seen in Fig.7.
Figure 7. Distribution of samples and boats with gray at specified points
The temperature of sulfur varied from 162 to 168 °C, in the average range it was 163 °C, which is recorded in Fig.8.
Figure 8. Stable temperature[7] of the region with a sulfur boat S.
The argon cylinder was opened at the level of 10 l/min, which ensured a stable gas flow[8] on the RRG BUIP unit in accordance with the task of 2 l/min, taking into account the features of the equipment[9] and a flow rate of 4 l/min, which is shown in Fig.9, respectively, and in Fig.10. A and B.
Figure 9. The level of the maximum possible gas supply on the Ar cylinder
a) b)
Figure 10. Parameters of input to the BP RRG: a) gas flow parameter, b) task parameter for the experimental installation during its work on obtaining ZnS
2. Results
Specially for this work, a two-zone laboratory installation has been developed, operating at low pressures with control of the inert gas flow rate.
The conducted studies allowed us to determine the optimal temperature and time regimes for the production of zinc sulfide, which can be defined as: zinc sulfidization temperature 450 0C, sulfidization time - 60 min, carrier gas flow rate 2 l/min, pressure - 100 mbar the production of zinc sulfide, which can be defined as: zinc sulfidization temperature 450 0C, sulfidization time - 60 min, carrier gas flow rate 2 l/min, pressure - 100 mbar
References:
- Chen R., Lockwood D. J. Developments in luminescence and display materials over the last 100 years as reflected in electrochemical society publications. J. Electrochem. Soc. 2002;149(9):S69-S78. DOI: 10.1149/1.1502258.
- Quan Z., Yang D., Li C., Kong D., Yang P., Cheng Z., Lin J. Multicolor tuning of manganese-doped ZnS colloidal nanocrystals. Langmuir 2009;25(17):10259- 10262. DOI: 10.1021/la901056d.
- Peng W. Q., Cong G. W., Qu S. C., Wan Z. G. Synthesis and photoluminescence of ZnS:Cu nanoparticles. Optic. Mater. 2006;29(2-3):313-317. DOI: 10.1016/j.opt-mat.2005.10.003.6.
- Debenham M. Refractive indices of zinc sulfide in the 0.405–13-μm wavelength range. Appl. Opt. 1984;23(14):2238-2239. DOI: 10.1364/AO.23.002238.
- Park W., King J. S., Neff C. W., Liddell C., Summers C. J. ZnS-Based photonic crystals. Phys. Stat. Sol. (b) 2002;229(2):949-960. DOI: 10.1002/1521- 3951(200201)229:2<949::AID-PSSB949>3.0.CO;2-K.
- Nanda J., Sapra S., Sarma D. D. Size-selected zinc sulfide nanocrystallites: synthesis, structure, and optical studies. Chem. Mater. 2000;12(4):1018-1024. DOI: 10.1021/cm990583f.
- Zhao Y., Zhang Y., Zhu H., Hadjipanayis G. C., Xiao J. Q. Low-temperature synthesis of hexagonal (wurtzite) ZnS nanocrystals.J. Am. Chem. Soc. 2004;126(22):6874-6875. DOI: 10.1021/ja048650g.
- Zoraida P. Aguilar, Chapter 2 - Types of Nanomaterials and Corresponding Methods of Synthesis,Editor(s): Zoraida P. Aguilar, Nanomaterials for Medical Applications, Elsevier, 2013, Pages 33-82,ISBN 9780123850898, https://doi.org/10.1016/B978-0-12-385089-8.00002-9.
- L.W. Cheriton, J.P. Gupta, BUILDING MATERIALS. in Encyclopedia of Analytical Science (Second Edition), 2005, Pages 304-314, https://doi.org/10.1016/B0-12-369397-7/00049-2