COLLECTION AND ANALYSIS OF DATA FROM THE EXPERIMENTAL COMPLEX AP7000, PROCESSING USING DEEP NEURAL NETWORKS
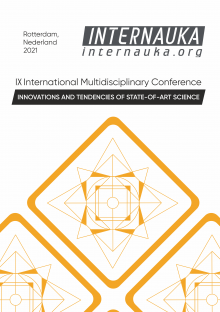
COLLECTION AND ANALYSIS OF DATA FROM THE EXPERIMENTAL COMPLEX AP7000, PROCESSING USING DEEP NEURAL NETWORKS
Maria Zolotukhina
Master in Computer Control and Information Processing in Technical Systems MIREA-Russian Technological University,
Russia, Moscow
Svyatoslav Zolotukhin
Bachelor's student in the specialty "Software Engineering" MIREA-Russian Technological University,
Russia, Moscow
ABSTRACT
The article discusses the collection and processing of vibration measurement data using the experimental complex AP7000, control sensors and classification of fault signals using deep neural networks. An example of diagnostic information with signs of defects in rotary equipment, training and test samples, neural network analysis of the spectra of vibration signals is also given.
Keywords: deep neural networks, training sample, control sensors, rotary equipment, data analysis, machine learning, vibration diagnostics, information processing.
To obtain high-quality samples of vibration signals with signs of malfunction, equipment with the ability to simulate the main types of defects in rotary equipment is needed [1]. This is the simulation complex AP7000 (shown in Figure 1). The stand presents an electromechanical rotor installation with the ability to simulate fault signals of rotating assemblies similar to the categories of faults in turbine generators of CHP, located on the territory of RTU-MIREA, Department of Automatic Systems.
Figure 1. Experimental stand AP7000
The stand uses non-contact eddy current sensor systems for measuring displacement (proximeters), shown in Figure 2.
Figure 2. Orthogonal placement
Signal processing was carried out in the zetlab program, based on the spectrograms of the signals, a training sample was compiled, shown in Figure 3.
Figure 3. Training sample
The creation of the vibration signal catalog was carried out according to the calibration scheme. It also consists of a set of faults at a separate time in the frequency range. The list of database criteria with information on 16 vibration sensors (vertical and horizontal vibration sensors on 8 supports) consists of:
Ve - Effective vibration velocity [mm / s]
V1 - Amplitude of the 1st harmonic of vibration velocity [mm / s]
phV1 - Phase of the 1st harmonic of vibration velocity [deg]
V2- Amplitude of the 2nd harmonic of vibration velocity [mm / s]
phV2- Phase of the 2nd harmonic of vibration velocity [deg]
V_LF- Low frequency vibration [mm / s]
V3 - Amplitude of the 3rd harmonic of vibration velocity [mm / s]
V4 - Amplitude of the 4th harmonic of vibration velocity [mm / s]
V5 - Amplitude of the 5th harmonic of vibration velocity [mm / s]
V6 - Amplitude of the 6th harmonic of vibration velocity [mm / s]
V7 - Amplitude of the 7th harmonic of vibration velocity [mm / s]
V8 - Amplitude of the 8th harmonic of vibration velocity [mm / s]
V9 - Amplitude of the 9th harmonic of vibration velocity [mm / s]
ADC_DC - DC component of ADC [b.r]
V_HF - High frequency vibration [mm / s]
S - The range of total vibration displacements [μm]
The file can contain up to 32700 records in total. The data obtained was classified into 10 classes and 500 by the signal of the available class. Any class is saved to a specific list. For the training sample, the labeled data are vibration velocities and vibration accelerations. It is necessary to optimize the criteria with input vectors and data processing results from vibration signals of rotary equipment generated in real time. The first stage includes processing input data with faults and with no interference in vibration signals and is used to combine processing algorithms, determine patterns and train the NSC.
The second stage is to assess the real situation of the rotary equipment when analyzing the output parameters. Classification and recognition of malfunctions is carried out, the presence of dangerous types of vibration signals with malfunctions is ascertained. The training samples obtained in the course of the experiment are saved in the database and will later be used for training the NSC and during the test control of the training stage [2]. Also, a database of dynamic characteristics of vibration measurements spectrograms (BDHV) is being prepared, which is a complete set of measurement samples obtained from 16 vibration velocity sensors installed on 8 turbo generator supports [3].
The input data of the neural network classifier will be spectrograms compiled from the results of vibration sensors measurements. Input data are csv files with measurements taken from 8 points, each of which has 2 sensors installed. The sensors measure both vertical and horizontal. For each direction, the following indicators were obtained:
Ve - effective speed,
V1, phV1 - amplitude and phase of the first harmonic,
V2, phV2 - amplitude and phase of the second harmonic,
V_LF - low frequency vibration,
V3, V4, ..., V9 - amplitudes of harmonics from 3rd to 9th,
ADC-DC- DC component of ADC,
V_HF - high frequency vibration,
SS - spread of total vibration displacements [4].
The output was:
• values of parameters of pre-processing algorithms;
• assessment of target indicators of the NSC performance;
• connected parameters of the learning process of the neural network classifier.
The output data was collected and stored in tabular form while the program was running on the computer's hard drive. The software runs on IBM compatible personal computers. The volume of the program is 105 MB. The file with the source code is 1.9 MB.
ACKNOWLEDGMENT
We would like to express our gratitude to MIREA - Russian Technological University to the Institute of Cybernetics and the Institute of Information Technologies for the opportunity to conduct research in the field of deep neural networks, vibrodiagnostics and IoT.
References:
- Okhtilev M.Yu. Intelligent monitoring technology and control of the structural dynamics of complex technical objects. /M. Yu. Okhtilev, B. V. Sokolov, R. M. Yusupov. - M .: Nauka, 2006 .-- 410s.
- V.A. Golovko, ed. prof. A.I. Galushkina Neural Networks: training, organization and application. - Moscow: IPRZhR, 2001
- Basics of vibration measurement - based on materials from DLI (under edited by V. A. Smirnov) [Electronic resource]. - Access mode to article: http://www.vibration.ru/osn_vibracii.shtml
- Goldin A.S. Vibration of rotary machines. M. Mechanical Engineering, 1999.