THE USE OF LITHIUM POLYMER BATTERIES IN ELECTRIC VEHICLES
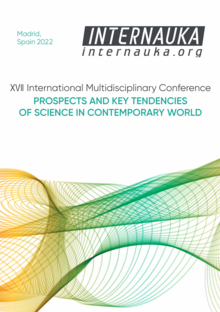
THE USE OF LITHIUM POLYMER BATTERIES IN ELECTRIC VEHICLES
Victoria Mikhaylenko
Student, Don State Technical University,
Russia, Rostov-on-Don
Yurii Kurnikov
Student, Shakhty Automobile and Road Construction Institute (branch) Platov South-Russian State Politechnic University (NPI),
Russia, Shakhty
Tatiana Nosacheva
Lecturer, Shakhty Automobile and Road Construction Institute (branch) Platov South-Russian State Politechnic University (NPI),
Russia, Shakhty
It is difficult to overestimate the value of transport for humanity. Since the beginning of time, it has played an important role, constantly developing and improving. The scientific and technological revolution, population growth, urbanization and many other factors in the 20th century have brought its development to an entirely new level.
At the same time, however, a problem has also arose: the sheer number of vehicles has caused environmental degradation on a global scale. That is why more and more attention is now being paid to the development of sustainable modes of transport.
Any transport that does not involve the combustion of hydrocarbons can be called pollution-free. The exception is nuclear reactions, which are not used in land transport. Biodiesel, internal combustion engine on the spirits also burn carbon, so they cannot be attributed to sustainable modes of transport. It is most correct to classify eco-transport by types of engines, but we will consider only one: the electric actuator.
It is currently the most rapidly developing type of environmentally friendly transport. It is destined for a great future, and all the major automobile manufacturers have already noticed it. Several thousand electric vehicles are already driving on the roads of the world. Moreover, the future electric car will not have such large dimensions and cost as the famous Tesla electric car. Rather, it will be some kind of rickshaw with a cab or a plain car body made of plastic. On average, an electric car needs to weigh four times less to compete with a gasoline-powered car. There are similar examples in the automotive industry.
The main problem with electric cars is batteries. They are already the only limitation to the mass production of electric cars. All other technical limitations were overcome 50 and 100 years ago. The electric motor has a higher efficiency than the gasoline one. Its resource is much higher, and the complexity of manufacturing is low. In addition, it does not require a gearbox. Now most electric cars are produced with lithium batteries. They have a very high price. Alternatively, I would like to suggest sulfur-sodium accumulators.
Work on replacing the liquid organic electrolyte in lithium-ion batteries with polymer electrolyte has been going on for a long time. This replacement eliminates electrolyte leakage and improves operational safety. The idea of a lithium polymer battery (Li-pol) is based on the phenomenon of transition of some polymers into a semiconductor state as a result of the introduction of electrolyte ions into them. The conductivity of polymers increases by more than one order of magnitude. To date, lithium current sources with electrolytes, which can be divided into three groups: dry polymer electrolytes; gel-polymer electrolytes formed by the introduction of a plastifier-solvent into the polymer; non-aqueous solutions of Li salts sorbed in the microporous polymer matrix, are developed and serially produced.
The researchers' efforts have been focused on finding polymer electrolytes for both lithium-ion batteries and lithium metal accumulators, whose theoretically possible energy density is several times greater than that of lithium-ion batteries.
By Nowadays, lithium current sources with electrolytes have been produced in series, and can be subdivided into three groups:
- dry polymer electrolytes (most often based on polyethylene oxide, in which various Li salts are introduced);
- gel-polymer homogeneous electrolytes formed by introducing a plasticizer-solvent into a polymer (or polymer mixture) with Li salts;
- non-aqueous solutions of Li salts sorbed in microporous polymer matrix.
Compared to liquid electrolytes in lithium-ion batteries, polymer electrolytes have lower ionic conductivity, which also decreases at temperatures below zero. Therefore, the challenge in the development of Li-pol batteries was not only to find an immobilized electrolyte with sufficiently high conductivity compatible with the electrode materials, but also to expand the temperature range of Li-pol batteries.
Modern lithium polymer batteries produce specific characteristics comparable to those of lithium-ion accumulators. Due to the absence of liquid electrolyte, they are safer to use than rechargeable lithium current sources. Li-pol batteries are compact and can be built in any configuration. Their case can be made of metallized polymer.
Operating current densities, however, are negligible, and the electrical characteristics of Li-pol batteries deteriorate markedly at lower temperatures due to crystallization of the polymer.
Both lithium-ion and metal anode batteries are being developed with gel-polymer electrolyte. The rather high current densities achieved and the extension of the operating temperature range allow such batteries to be used for a wide range of portable equipment, cell phones, laptops, digital photographic equipment, etc.
Gel-polymer electrolyte batteries are produced by many companies around the world. Electrode materials, electrolyte compositions and Li-pol battery manufacturing technologies vary greatly from company to company. Their characteristics also vary.
All developers note that the quality of Li-pol accumulators and the operation stability is greatly affected by the homogeneity of the polymer, which is influenced by both the ratio of electrolyte components and the temperature of polymerization.
Taking into account that the possibilities of creating lithium-polymer accumulators in a wide range of capacities have already been really shown, and the fact that Li-pol batteries have significantly higher performance in all standard tests for safety of use (overcharge, forced discharge, short-circuit, vibration, crushing and piercing with a tack) compared to lithium-ion batteries with liquid electrolyte. The prospects of serious expansion of Li-pol batteries production and their use in a wide variety of technical spheres do not raise any doubts.
Sometimes to reduce the internal resistance of Li-pol batteries, helium electrolyte is added. Most lithium polymer batteries used to power cell phones are actually hybrid batteries, which are something in between lithium ion and lithium polymer accumulators, with a helium electrolyte.
What is the difference between lithium-ion rechargeable batteries and lithium polymer ones with helium electrolyte? Although their characteristics are similar, lithium polymer batteries use a solid electrolyte instead of separators. The helium electrolyte added to them is simply designed to improve their ion-exchange processes and thus lower their internal resistance.
Comparative safety tests were performed on two types of prismatic lithium-ion batteries: with liquid and gel-polymer electrolytes (Table 1). No special measures were taken to ensure the safety of the accumulators. The batteries were tested by needle puncture, heating to 200 °C, short-circuiting, and very high recharge (up to 600%). According to the table, the safety of lithium-ion batteries with polymer electrolyte is much higher than that of accumulators with liquid electrolyte.
Table 1.
Safety tests
Type of test |
The battery with gel-polymer electrolyte |
The battery with liquid electrolyte |
Needle puncture |
No change |
Explosion, smoke, electrolyte leakage, temperature increase to 250 °С |
Heating up to 200 °С |
No change |
Explosion, electrolyte leakage |
Short circuit current |
No change |
Electrolyte leakage, temperature increase to 100 °С |
Overcharge (600%) |
Bloat |
Explosion, electrolyte leakage, temperature increase to 100 °С |
Based on all of the above, we can conclude that a reliable and safe fuel for the electric drive of cars will be the use of Li-pol batteries. But the problem is that in contrast to liquid or gaseous fuel, the battery power cannot be charged in such a short time.
To solve this problem, we suggest using Li-pol batteries with a quick-release mechanism. By installing them in independent blocks of small size, this is done to reduce the weight of a single battery, which will allow in the case of mortality of one of the accumulators to quickly replace it.
Each battery unit has 2 through-holes with contact pieces. The battery packs are placed on the electric-powered contacts and bolted to the cap. It is also structurally possible to set the blocks by placing the accumulators one on top of the other and fixing them with bolts to each other. The conventional scheme of the battery pack is shown in Figure 1, where 1 and 2 - contact parts (slots for the power contacts), 3 - bolt fastening, 4 - handles for easy removal/installation of the battery pack.
a) Top view b) Side view
Picture 1. Schematic diagram of one battery pack
The filling stations should be equipped with warehouses for storing charged accumulators, and automated installers. The "charging" process at the station will occur as follows:
1) The car drives to the filling station
2) Discharged batteries are removed
3) Batteries are taken to the charging and recharging station
4) Charged batteries are installed
5) Payment
Removed discharged batteries are placed on the charger and at the end of the charge are sent to the warehouse for storage and subsequent installation in other vehicles.
This concept requires the production of unified battery packs so that drivers do not have to think about what type of pack they need for their vehicle and whether they will have them available. To maintain economy and competitiveness, it is possible to equip units with different internal designs (Li-pol, Li-ion, etc.).
To safely remove/install the units to avoid sparking and human electrocution, the contact power contacts are disconnected from the vehicle's mains, and then reconnected to the circuit.
References:
- Journal. Sezony goda. [Seasons of the year]. Available at: https://sezony-goda.rf/ekotransport.htm
- Litii-polimernye akkumulyatory. [Lithium polymer batteries] Available at:http://autoeco.info/lipol.php
- Kolosnitsyn V.S., Dukhanin G.P., Dumler S.A., Novakov I.A. Polimernye elektrolity dlya litievykh i litii-ionnykh khimicheskikh istochnikov toka. [Polymer electrolytes for lithium and lithium-ion chemical current sources]// «Izvestiya» Volgograd State Technical University – №2 – 2004
- Skundin A.M., Yarmolenko O.V. Sovremennoe sostoyanie i perspektivy razvitiya issledovanii litievykh akkumulyatorov. [State of the art and prospects for lithium battery research] // Uspekhi khimii. [Advances in chemistry] — 2002, — № 4. — Vol. 71.
- Brovka N. Sistemy kontrolya litii-ionnykh i litii-polimernykh akkumulyatorov. [Li-ion and lithium polymer battery monitoring systems] // Komponenty i tekhnologii [Components and technologies]. — №10 – 2006