ANALYSIS OF A TABLET MACHINE FOR PRESSING POWDER RAW MATERIALS
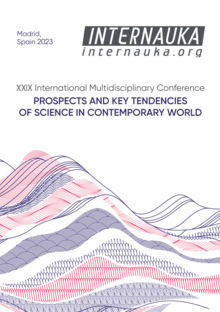
ANALYSIS OF A TABLET MACHINE FOR PRESSING POWDER RAW MATERIALS
Ashok Tivari
General Director of the company «Shayana Farm», Master Tashkent State Technical University,
Uzbekistan, Tashkent
Jasur Safarov
DSc, professor Tashkent State Technical University,
Uzbekistan, Tashkent
Shakhnoza Sultanova
DSc, professor Tashkent State Technical University,
Uzbekistan, Tashkent
In modern pharmaceutical production, tableting is carried out on special rotary tablet presses (RTM). In world practice, high-performance tablet presses have been created, equipped with devices for automatic control of tablet weight and pressing pressure.
The technological cycle of tableting on the RTM consists of a number of successive operations: dosing of the material, pressing (formation of a tablet), its ejection and dropping. All of the above operations are carried out automatically one after another using the appropriate actuators [1-2].
1-boot agitator; 2-filling agitator; 3-dosing agitator.
Figure 1. The device of a three-chamber feeder-dispenser
Tablet machines use a volumetric dosing method. The RTM loading device consists of a loading funnel - a hopper and a feeder-dispenser, fixed motionless on the machine frame. The hopper ensures the continuity of the tableting material flow. For uniform supply of poorly flowing materials from the hopper to the feeder, the former can be equipped with mixers, augers, agitators. The feeder-dispenser is designed for the formation, direction and dosed supply of the tablet mixture to the pressing zone.
The design of the feeder should ensure the operation of the RTM with high productivity, the accuracy and stability of the weight of tablets, the tableting of materials with different properties and characteristics, the filling of matrix holes from minimum to maximum diameters corresponding to the size of tablets according to the requirements of the Pharmacopoeia.
In domestic RTM, feeders-dispensers are used: bladed 2- and 3-chamber and frame. The most widely used 2-chamber feeders. High-performance machines with a capacity of 300,000 tablets per hour or more are equipped with 3-chamber dosing feeders with the best characteristics for filling RTM matrices. The stability of the mass of tablets during the operation of a 3-chamber feeder-dispenser is explained by its design (Fig. 1), in which, in comparison with 2-chamber ones, there is an upper chamber with the blades of the loading agitator (1), located above the two lower chambers with filling (2) and dosing (3) agitators. It serves to transfer the tablet mixture from the hopper to the chamber of the filling agitator (2) and regulate its flow to the feeder depending on the change in material consumption.
Blade dosing devices, which include 2- and 3-chamber feeders, despite the advantages, have a high metal content, are equipped with an individual drive, which leads to increased energy consumption, and are not easy enough to operate when changing drugs.
The simplest and most reliable in operation is a frame feeder, but its use is effective only when pressing preparations of good and medium flowability at a rotor speed of up to 30 m/min. At present, a design of a frame feeder with a vibrating mesh has been created. The size of the grid is selected depending on the shape and size of the granules, the flowability of the tablet mixture. By changing the amplitude and frequency of vibrations of the vibrating grid, it is possible to achieve high accuracy of the tablet mass in all operating modes of the RTM, while maintaining all the positive performance characteristics of the frame feeder.
1-lower; 2-upper. One-piece punches 3 and 4 with a flat surface, 5 and 6 with a spherical surface
Figure 2. Punches of tablet machines
Pressing on tablet machines is carried out with a press tool consisting of a matrix and two punches.
Matrix is a steel part, as a rule, of a cylindrical shape with a through cylindrical hole with a diameter of 3 to 25 mm. Matrices are inserted into the corresponding holes of the rotor rotating on a vertical shaft. The rotor speed of modern RTM is in the range from 15 to 75 min, the number of matrices reaches 41-75.
Punches (upper and lower) - these are cylindrical rods (pistons) made of chrome steel, which enter the holes of the matrix from above and below and ensure the pressing of the tablet under pressure. The pressing surfaces of the punches can be flat or concave (of different radii or curvature), smooth or with transverse grooves (notches) or with an engraved inscription. Punches differ in the way they are connected to the pusher: they can be solid or prefabricated (Fig. 2). The solid punch is one piece with the pusher. It is easier to manufacture, but more expensive to operate, since the punch wears out faster than the pusher, and when it is replaced, the pusher also changes. The methods of connecting the punch with the pusher in the prefabricated press tool in machines of different companies are different. The general view of the RTM-41 is shown in fig. 3, and the tableting process can be seen on the cyclogram - a sweep of the machine (Fig. 4).
Figure 3. Rotary tablet machine A-41
From the hopper (1), the powder flows by gravity into the feeder-dispenser (3), which is fixedly fixed on the machine frame. The filling agitator with blades (4) feeds the powder into the matrix (6), while the punches (8) fixed in the pushers (9) descend along the fixed copier (10) and the adjustable copier (15) to the full depth of filling the matrices. With further rotation of the rotor, the pusher follows the horizontal section of the copier to the dosing mechanism, which consists of a copier (16) and an adjustable dispenser (17) hinged to it. The copier-dispenser moves the pusher with the punch up, raising the powder in the matrix to a height corresponding in volume to the given tablet weight. At this time, the blades (20) of the dosing agitator cut off the excess dose and transfer it back to the zones ; action of the filling agitator. Since the blades are 1.0-1.5 mm higher than the bottom of the feeder housing, the edge of the feeder housing (21) is also involved in dosing, which is 0.1 mm away from the table mirror. The knife (22) with a PTFE plate tightly pressed against the table finally cuts off the dose [1-2].
Figure 4. The principle of operation of rotary tablet machines - 41
During the further transfer of the dose, the lower pusher hits the horizontal copier (18), the upper one passes under the bumper copier (23), which lowers the upper punches until they enter the matrix. The rollers (19) carry out pre-compression (pre-pressing ), and the pressure rollers (11) carry out the actual pressing. At the same time, the powder is kept under pressure on the RTM due to the presence of a flat end on the pusher head, displacement of the axes of the upper and lower pressure rollers by 3-4 mm, introduction of special copiers (2) placed at the level of the pressure roller at the time of pressing. The ejection of the tablet from the plane of the matrix onto the surface of the table mirror is carried out by an ejection mechanism consisting of three elements. The ejection roller (12) lifts the tablet from the die wall. The ejection copier (13) brings the tablet to the upper level, and the ejector (14) is adjusted in such a way that the tablet is removed from the matrix to the table surface, then the tablet (7) is brought to the knife (5) by the rotor, which directs it to the tray and then to the receiving container [1-2].
Tablet machines are equipped with a device for collecting losses of tablet mass during manufacture and packaging, equipped with devices for automatic control of tablets for metal inclusions, which not only detect, but also remove tablets with metal inclusions from the flow. The minimum size of detectable metal inclusions is 0.5 mm at an average continuous tablet flow rate of 100,000 pieces per hour.
References:
- Electronic resource: https://studfile.net/preview/6065996/page:55/
- Busignies V. Recherche de lois de mélange sur des proprietes mecaniques de systems granulaires compactes . PhD, Université Paris XI - Faculté de pharmacie de Châtenay-Malabry , 2005.