CONSTRUCTION OF ACTIVE WORKING MACHINES FOR THE CARE OF SEEDLINGS
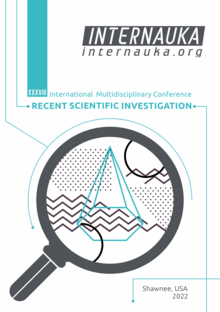
CONSTRUCTION OF ACTIVE WORKING MACHINES FOR THE CARE OF SEEDLINGS
Alexander Zhirnov
Doctor of Technical Sciences, Professor, Federal State Budgetary Educational Institution of Higher Education “Far Eastern State Agrarian University”,
Russia, Blagoveshchensk
ABSTRACT
This scientific work presents the problem of processing seedling row spacing in forest schools. The article introduces research in the field of technology development and the working machine involved in this process. The processes of influence of working bodies on the physical and mechanical properties of the soil, plant residues in the soil are highlighted. A classification of active working bodies, existing tillage machines and the proposed machine with a new active working body is given. Special attention is paid to the working depth and the quality of the tillage machine. A feature of the technological process of soil cultivation with an active working body is the setting of the front and rear cutting angles. A constructive-technological scheme of a machine for agrotechnical care of forest crops with active working organs has been developed. The novelty of the design of the working bodies lies in the fact that in one pass it carries out additional tillage and removal of trees and shrubs. A mathematical model of the interaction of the working body with the processed medium and dynamic processes in the mechanical drive of the machine was developed, taking into account the parameters of the working body and the physical and mechanical properties of the growth, which made it possible to establish the use of a new design of the cutter, confirmed by the patent, allows solving two scientific problems in the field of soil cultivation: changing the cutting angle, depending on the type of soil and improving the quality of the soil, which is guaranteed to affect the qualitative growth of forest plantations
Keywords: schools for forest crop seedlings, tillage machines, active working bodies, cutting angles, root system.
Figure 1. General view of the unit for weeding seedlings
1 Introduction
The aim of the work is to increase the efficiency of agrotechnical care of forest crops in schools by substantiating the main parameters of the working organs of active action, ensuring the destruction of weed growth with simultaneous additional tillage[1,2]. In accordance with the Forest Code of the Russian Federation, a necessary condition for the successful cultivation of forest crops in schools is agrotechnical care for them. Agrotechnical care is carried out in order to prevent overgrowth of the surface of the soil by weedy herbaceous and the accumulation of moisture in the soil, etc[3].
One of the most important technological operations in the cultivation of agricultural crops is tillage, which must be performed in a short agrotechnical time and with the required quality. The quality of processing plays an important role in increasing the productivity of agricultural crops. Among the tillage operations, pre-sowing treatment has the greatest impact on the yield of agricultural crops. Pre-sowing preparation of the soil is achieved as a result of the following technological tasks: loosening( crumbling), mixing, formation of microrelief, compaction, creation of the required addition and structure of the treated soil layer, etc. It is established that the most favorable conditions for the growth and development of grain crops are achieved with heterogeneous addition of the treated soil layer.
The variety of tasks of tillage requires the presence of a huge number of various tillage tools with various working bodies, the possibility of using which also depends on specific soil and climatic conditions and the initial state of the soil. Mechanical tillage is an important link in the farming system of any economy. In modern technologies of cultivation of agricultural crops, tillage accounts for 35-40% of energy and 25-30% of labor costs. Physical, agrochemical and biological indicators of soil fertility depend on soil cultivation, which largely determine the size and quality of the future crop. In the process of mechanical tillage, several main elements take part: a traction vehicle, an agricultural machine or tool, and the material being processed, i.e. the soil. The working body of the machine affects the soil in one way or another and changes its properties and structure. Mechanical tillage is the impact on it by the working bodies of machines and tools in order to create optimal conditions for the life of agricultural plants, increase fertility and protect the soil from water and wind erosion.
It is necessary to take into account all the factors that affect the technological process. These are the depth of processing, the speed of movement, the agrotechnical properties of the soil before and after processing, and the geometric parameters of the working body itself. At the same time, it is necessary to take into account such an indicator as the coefficient of terradynamic resistance, which will depend on the shape of the working body (the shape must have the smallest permissible area of the frontal projection).
Theoretical and experimental studies of the tillage process are associated with great difficulties and difficulties due to the variety of soil properties and the inconsistency of the tasks: in conditions of wide fluctuations in soil and climatic factors, it is necessary to improve the quality of tillage while reducing its energy intensity. However, at the present time there is a clear gap between the theory of tillage and its practical implementation, since there has been no significant progress in the theory of tillage over the past 20 years. Despite all the efforts of scientists and designers, the problem of guaranteed high-quality tillage has not yet been solved. A comprehensive solution to the problem of tillage, including improving the quality while reducing the energy intensity of its processing, with sufficient reliability of tools and machines has not yet been found. Currently, the efforts of designers of tillage tools and machines are mainly aimed at reducing the specific energy intensity of tillage. This is often achieved not only by improving the design and operating parameters of tools and machines, but also by reducing the quality of tillage, referring to agrotechnical requirements. The soil structure created by modern tillage tools and machines does not correspond to the optimal one for plant development. It can only approach it to a greater or lesser extent.
For the mechanization of agrotechnical care of crops in schools, various means of mechanization are currently used[4,5], such as milling machines, cultivators with passive working bodies, and others[6]. Disc plows and harrows crush weeds well and embed it to a certain depth, but they are very energy intensive and require two passes in cross directions[7]. To cultivate the soil between the rows of forest crops in schools with the simultaneous destruction of weeds and roots, milling cultivators are used[8], which provide good quality loosening of the soil, crushing and embedding of herbaceous vegetation (Fig. 1).
The following requirements are imposed on cultivators for row-to-row tillage in forest nurseries:
- damage to planted plants
- should not exceed 1%;
- deviation of the processing depth-no more than ± 2 cm;
- complete destruction of weeds;
- no removal of the wet soil layer to the surface
The working body of milling cultivators of the CFP-1.5 type is a drum with knives and a drive from the tractor power take-off shaft. Thanks to the active drive of the working bodies, such cultivators provide good loosening of the soil and a high degree of destruction of weed vegetation. However, when working, they can damage up to 5 % of the planted plants. In addition, milling cultivators have a complex design and a high energy consumption of the process due to the presence of a drive of working bodies. Therefore, despite some of their advantages, they have not found wide application.
Cultivators with passive working organs have received the greatest application for agrotechnical care of plants, both in the sowing and in the school departments of the nursery. These cultivators have a set of replaceable working bodies and fully meet the requirements imposed on them.
Cultivators of the Shadrin design (KPSh-1,25, KPSh-1,4 and KPSh-1,5) are mounted on the frame of the T-16M self-propelled chassis and are equipped with working bodies in the form of pointed paws and curved needle disks of the original design. However, these cultivators are designed for the care of plants with a certain placement of rows on the tape, and their design does not allow you to rearrange the working bodies to work according to other sowing or planting schemes. This limits the possibilities of their operation.
Replaceable working bodies are mounted on a transverse beam with the help of mobile crowns. This attachment allows you to arrange the working bodies for any scheme of placing plants on the tape.
Replaceable working bodies include narrow-grip hollow paws, ripping chisels, needle discs and universal pointed paws.
Needle discs are advisable to use for the destruction of the soil crust when caring for 1-year-old seedlings. At the same time, they partially (up to 30 %) remove weeds and loosen the soil to a depth of 6 cm. The diameter of the needle disks is 300 mm, the width of the disk capture is 22 mm. The disks are assembled in sections of 2 pcs. in each with a distance of 50 mm between them and are mounted on special brackets.
Narrow-grained hollow paws are most effective when caring for 2 - and 3-year-old seedlings, as well as when working in the school department of the nursery. In the processing zone (about 12 cm), they ensure the complete destruction of weed vegetation and loosening of the soil to a depth of up to 8 cm. The protective zone is 4-6 cm, which is quite acceptable when caring for plants in the nursery. When caring for seedlings, especially on heavy soils, it is advisable to use loosening chisels.
Universal pointed paws are installed on the track of the wheels of the chassis and process the inter-tape space. With repeated processing of the site, it is necessary to use different working bodies, i.e. alternately change them
Figure 2. Tillage unit with an active working body for weeding seedlings in schools, based on a brush cutter
2 Materials and Methods
In accordance with the Forest Code of the Russian Federation, a necessary condition for the successful cultivation of forest crops in schools is agrotechnical care for them. Agrotechnical care is carried out in order to prevent overgrowth of the surface of the soil by weedy herbaceous and the accumulation of moisture in the soil, etc[9,10]. For the mechanization of agrotechnical care of crops in schools, various means of mechanization are currently used[11,12], such as milling machines, cultivators with passive working bodies, and others. Disc plows and harrows crush weeds well and embed it to a certain depth, but they are very energy intensive and require two passes in cross directions. To cultivate the soil in the aisles of forest crops in schools with the simultaneous destruction of weeds and roots, milling cultivators are used, which provide good quality loosening of the soil, crushing and embedding of herbaceous vegetation (Fig. 2).
Figure 3. Active working bodies of the existing cutter mechanisms
However, they have insufficient reliability when encountering obstacles due to breakdowns of knives, cardan shafts and other elements of the hydraulic drive, and also differ in the high energy consumption of the working process. In the conditions of schools[13], working machines with active working bodies in the form of cylindrical cutters, disk and chain saws also do not fully meet the necessary requirements for the care of forest crops, since they cut weeds at a height of 1.5-3.5 cm, as a result of which it is resumed quite quickly[14], and their hydraulic drive is not reliable enough(Fig.3). Thus, based on the analysis, it follows that in the designs of the working bodies of small-sized tillage cutters, from the point of view of ensuring the lowest energy consumption when milling the soil and observing the conditions of the course stability of the machine, it is more expedient to use knives with an upper sharpening[15]. In addition, to obtain the greatest effect of reducing energy consumption, it is recommended to use working bodies with a constant cutting angle.
Figure 4. Geometry of cutting bodies: 1) with front cutting angle, 2) with rear cutting angle
Therefore, it becomes necessary to create machines with active working bodies for cutting weeds at the level of the root system and simultaneous additional tillage in schools, in one pass of the unit (Fig. 4).
Based on the processing of data from various firms on the design of milling machines, a number of dependencies were obtained that characterize the technological and energy parameters of the active working body[16].
Thus, on the basis of the analysis carried out, it follows that in the designs of the active working bodies of small-sized tillage mills, from the point of view of ensuring the lowest energy consumption when milling the soil and observing the conditions for the machine's directional stability, it is more expedient to use knives with top sharpening[17].
3 Results
At the heart of a working machine with an active working body, a motor-brush cutter engine with cutter bodies was used. The choice of the thickness and width of the active working body depends on its strength and is determined from the corresponding strength calculations. To ensure the strength of the structure, the taper angle must be done in the range of 15-20 ° (Fig., 4,5.) Conducted theoretical studies on setting the rear cutting angle ε of a symmetrical working body showed that the least resistance occurs when ε is equal to 3-5 °. With a decrease in the angle ε to 0 °, there is a great resistance to friction by the occipital part of the organ against the wall of the furrow of uncultivated soil. With an increase in the angle ε from 5 ° to 15 °, there is a sharp increase in the friction of the cut soil against the front edge of the knife in a linear dependence on the cutting angle. When cutting, due to elasticity, the soil rises slightly following the cutting edge of the organ, therefore, when the rear cutting angle ε is equal to 2-3 °, the soil grazes against the lower edge. In this case, constant wear of the member occurs, therefore, it is impossible to set the clearance angle less than 7 (Fig. 4) °. It is not recommended for stable cutting of the organ's soil to take the clearance angle of at least 10 °. Therefore, for working bodies, on average, the rear cutting angle is recommended to be taken within 8-12 °. From the analysis of the effect of the sharpening angle, taking into account the peculiarities of its work, it follows that in order to ensure self-sharpening of the working bodies, the lower sharpening is mainly used, while with the aim of to reduce energy consumption it is more expedient to use the upper sharpening of the working body (Fig. 5).
Figure 5. Scheme of tillage with an active working body
4 Discussion
In all cases, the value of the cutting angle α is minimum when the knife approaches the soil surface and is maximum when it leaves the soil. It is also seen that for a knife with an upper sharpening, the cutting angle at the maximum and minimum translational speed of the cutter will be the smallest in comparison with a knife with a lower sharpening. This leads to significant scattering of the cultivated soil and an increase in energy consumption, and sometimes to pushing the drum drum out of the soil and disrupting its directional stability therefore, taking into account the design features and the use of small-sized tillage mills as their working bodies top-sharpened knives are preferred (Fig. 5). The main disadvantage of using existing small-sized milling cutters at a constant cutting angle, in our opinion, is the unevenness of the soil in terms of the texture and type of soil. To solve this disadvantage, a design of a cutter with a variable cutting angle has been developed, with a pressure sensor installed on the cylinder rod, and a control mechanism for changing the cutting angle. This allows us to solve two scientific problems in the field of soil cultivation: a smooth change in the cutting angle, depending on the type of soil and an improvement in soil quality, which is guaranteed to affect the qualitative growth of forest plantations.
Conclusions
A design-technological scheme of a machine for agrotechnical care of forest crops with active working organs has been developed. The novelty of the design of the working bodies, which in one pass carries out additional tillage and removal of trees and shrubs. A mathematical model of the interaction of the working body with the processed medium and dynamic processes in the mechanical drive of the machine has been developed, taking into account the parameters of the working body and the physical and mechanical properties of the growth, which made it possible to establish that - reducing the width of the cutting element has a greater effect on reducing the cutting force than reducing the sharpening angle of this element. So, for a growth d = 2 cm, with a cutting edge width b = 1.2 cm, sharpening angle = 20 °, cutting force Pres = 320 N; at b = 1.2 cm, = 30 °, Pres = 540 N; at b = 0.5 cm, = 20 °, Pres = 520 N; at b = 0.5 cm, = 30 °, Pres = 670 N; - when cutting off a growth with a diameter of 0.4 cm with a working body 0.5 cm thick, with a sharpening angle of 35 °, with a change in the cutting depth from 4 to 15 cm, bending stresses increase 1.5 times, reaching a value of 5 MPa; - the ultimate strengths for cutting the stems and roots of the shoots were, respectively, 64% = 3.3 MPa, 64% = 3.34 MPa. The use of a new design of the cutter, confirmed by a patent, allows to solve two scientific problems in the field of soil cultivation: a smooth change in the cutting angle, depending on the type of soil and an improvement in soil quality, which is guaranteed to affect the qualitative growth of forest plantations.
References:
- Макаренко А.Н. Обоснование параметров рабочих органов почвообрабатывающих машин с переменными углами рабочих поверхностей /А.Н. Макаренко//Актуальные направления научных исследований XXI века: теория и практика. 0. Т. 2. № 5-3. -Воронеж: Издательство Воронежской государственной лесотехнической академии, 2014. -С. 236-240. DOI: 10.12737/6971
- Повышение эффективности крошения почвы стрельчатой лапой и ее долговечности при формировании геометрии рабочей поверхности армирующей наплавкой /Бонда-рев А.В., Борозенцев В.И., Макаренко А.Н. и др.-Москва; Белгород: ОАО «Центральный коллектор библиотек «БИБКОМ», 2015. -149 с. DOI: 10.15217/B978-590556353-9
- Валиев, А.Р. Исследование процесса движения почвы по рабочей поверхности дискового культиватора / А.Р. Валиев // Вестник Казанского государственного аграрного университета. - 2017. - Т. 12. - № 3 (45). - С. 54-60. DOI: 10.12737/article_5a1d9587a0d852.23012684
- Theoretical fundamentals for determining soil erosion potential. Periódico Tchê Química: órgão de divulgação científica e informativa [recurso eletrônico] / I. Maksimov, N. Adigamov, A. Mustafin, et al. // Grupo Tchê Química. 2019. Vol. 16 No. 31. P. 540-557
- Яхин, С.М. Кинематика игольчатого эллипсовидного диска ротационного почвообрабатывающего орудия / С.М. Яхин, И.И. Алиакберов, Л.М. Нуриев, Ф.Ф. Яруллин // Техника и оборудование для села. - 2020. № 2 (272). С. 12-15. DOI: 10.33267/2072-9642-2020-2-12-15
- Результаты экспериментальных исследований ротационного конического рабочего органа в почвенном канале / А.Р. Валиев, Ф.Ф. Яруллин, Р.И. Ибятов и др. // Вестник Казанского ГАУ. 2014. №3 (33). С.78-85. DOI: 10.12737/7153
- Yarullin F., Valiev A., Muhamadyarov F., Ziganshin B. Determination of energy characteristics of conical rotary working tool for tillage. 19th International Scientific Conference Engineering For Rural Development Proceedings, Volume 19 May 20-22, 2020 / Latvia University of Life Sciences and Technologies Faculty of Engineering, Jelgava, 2020 - P. 1069 - 1075. DOI: 10.22616/ERDev2020.19.TF252
- Mukhametshin I., Valiev A., Muhamadyarov F., Kalimullin M., Yarullin F. Kinematic analysis of conical rotary subsoil loosener for tillage. 19th International Scientific Conference Engineering For Rural Development Proceedings, Volume 19 May 20-22, 2020 / Latvia University of Life Sciences and Technologies Faculty of Engineering, Jelgava, 2020 - P. 1946 - 1952. DOI: 10.22616/ERDev.2020.19.TF553
- Джабборов Н.И., Эвиев В.А., Сергеев А.В., Семенова Г.А. Оценка вероятностно-статистических характеристик тягового сопротивления почвообрабатывающего агрегата с динамичными рабочими органами // Известия Нижневолжского агроуниверситетского комплекса: Наука и высшее профессиональное образование. 2019. № 2(54). С. 275-284. DOI: 10.32786/2071-9485-2019-02-33
- Зволинский Н.В. Автоматизация управления работой садовой фрезы / Н.В. Зволинский, М.А. Мосяков // Сельскохозяйственные машины и технологии. 2018. Т.12. №6. - С. 15-19. DOI: 10.22314/2073-7599-2018-12-6-15-19. DOI: 10.22314/2073-7599-2018-12-6-15-19