FEATURES OF WIRING AND COMPLETION OF WELLS IN NON-GAS FIELDS OF TURKMENISTAN USING ADVANCED TECHNOLOGIES
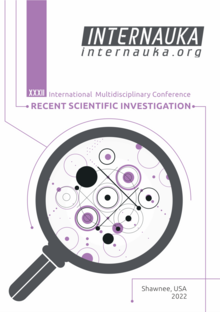
FEATURES OF WIRING AND COMPLETION OF WELLS IN NON-GAS FIELDS OF TURKMENISTAN USING ADVANCED TECHNOLOGIES
Annaguly Deryaev
Candidate of Technical Sciences, Senior Researcher, Scientific Research Institute of Natural Gas of the State Concern „Turkmengas”,
Turkmenistan, Ashgabat
ABSTRACT
The economic effect of the introduction of the technology of dual completion was obtained mainly by reducing the cost of drilling additional wells, as well as by a second additional elevator, which in turn makes it possible to shorten the payback period and reduce operating costs.
Keywords: two-lift method, saturation, waterlogging, anti-blowout equipment.
In the oil and gas fields of Turkmenistan, one of the most priority tasks being solved today to increase oil production volumes is the comprehensive modernization of production, the widespread introduction of new technologies and highly efficient equipment. The use of the latest technologies helps to increase the production potential both by extracting hard-to-reach oil from long-exploited fields, and by putting into development previously inaccessible deep-lying oil horizons. Currently, the oil industry of Turkmenistan is facing the issue of involvement in the active development of hard-to-recover oil reserves, the bulk of which is located in low-permeability reservoirs. The importance of solving this problem is determined by the depletion of reserves in long-exploited areas with a sharp decrease in well productivity [1].
Dual completion (DC) in foreign practice is widely used with the introduction into practice of drilling inclined and horizontal wells, where a reduction in the cost of oil production and an increase in the coefficient of hydrocarbon extraction has been achieved.
The experience of drilling such wells in various countries over a number of years has shown that the following is necessary for successful and economically justified drilling:
- high engineering qualification of the staff;
- availability of reliable geological data that are necessary for the design and wiring of a particular well;
- creation, development, production and application of special devices and equipment;
- latest software;
- the use of special drilling fluids in some cases;
- new technologies and devices for well completion.
Most of the oil and gas fields of Southwestern Turkmenistan, in particular Goturdepe, Northern Goturdepe and Barsagelmez have a multi-layer structure, that is, hydrocarbons are located on different horizons, each of which has its own characteristics (reservoir pressure, permeability, saturation pressure, water content). Productive horizons have different capacities from one to several tens of meters, their operation is carried out from the bottom up.
The traditional scheme of exploitation of such deposits provides for the development of a grid of vertical wells for each operational facility, which leads to an increase in capital costs for drilling wells and a decrease in the profitability of the products obtained. Accordingly, in the production of hydrocarbon raw materials, the main cost item is the construction of new production wells. It is necessary to solve the problem of reducing construction costs almost immediately with the introduction of wells into drilling. The simplest way is to combine several oil-saturated horizons into several development objects.
The latter is necessary as a means to significantly increase the probability of reaching the design mark (reducing the likelihood of well loss for technical reasons). Exceptional attention is paid to drilling technology, including the quality of drilling mud, drilling modes, and issues of qualitative separation of formations. The success of the wiring of such wells is largely determined by the preparation for its drilling (design and planning of work before drilling) and operational planning to optimize decision-making during drilling. For this purpose, when designing such drilling, and including planning the multi-layer operation of the well, it is necessary to use a computer with special software packages, including a serious database and knowledge base, for the objects to be developed. In the presence of data on productive formations, it is necessary to choose the most economical technology, which is determined by the target task that the mining company sets before drilling, the properties of the formation and drilling conditions during the work. The most important factor of any project is engineering planning of processes using advanced technologies. In order to avoid undesirable consequences due to poor work planning, it is necessary to use the engineering knowledge of the processes of its specialists.
Considering the world experience of field development with the use of dual completion (DC) of two or more horizons in one well, he prefers the use of special equipment lowered into the well and exploiting several productive layers. The main element of such equipment is a packer that isolates the layers from each other, gas lift valves for gas supply during the gas lift method of extraction and separate channels for oil to reach the surface. The requirements for equipment for separate operation should allow the implementation of the same technological measures as when opening these layers with separate wells [2].
Considering the proposals of world manufacturers of downhole equipment for dual completion, oil engineers focused their attention on the equipment of the Weatherford company. The scheme of simultaneous oil production with the use of technological equipment using a combination of the fountain method with the subsequent transition to the gas lift method was chosen. According to the design, a two-lift method was adopted dual completion of several oil reservoirs. The essence of this technology lies in the fact that two parallel tubing elevators are lowered into the operational column (mainly a 244,5 mm intermediate column), differing in suspension height - short and long. At the same time, productive horizons are separated by a packer device, which ensures their separate operation and accounting of production by the well for each operational object [3].
Wells №№147, 37, 200 and 201 were laid at the field in the order of field tests, where technological equipment was supposed to be used dual completion. Upon completion of the construction of wells and the introduction of technological innovations in the development of fields by the technology of dual completion (DС) of several productive horizons, with two tubing elevators, large volumes of oil were received in three wells (well №201 is in drilling), which confirmed the economic feasibility of using the selected downhole equipment. At well №147, an oil inflow of 800 tons/day was obtained, and at well №37, the oil inflow was 730 tons/day [4]. This is several times higher than the average values at the exploited fields, which in practice confirms the forecasts of the concern's specialists about the high prospects for the development of deep-lying deposits of the Goturdepe field.
It should be noted that the Goturdepe field, which has been developed for more than 50 years, thanks to the introduction of new technologies, today not only continues to be successfully operated, but also increases its oil recovery.
The achieved success is due, first of all, to the use of modern powerful drilling equipment, highly efficient technologies that are mastered by the concern's specialists.
Thus, successfully implemented new technologies and equipment in the process of drilling and development of wells contributed not only to improving the quality and shortening the construction time of wells, but also to a significant increase in oil production.
Despite the fact that the first experience of using the DC technology had a positive result, not all technical problems have been completely solved and it is necessary to work out this technology and bring it to perfection.
As for the Northern Goturdepe field, an additional difficulty for the additional exploration and development of the area is the fact that some of the points on the exploration and development grid are located in the waters of the Balkhan Bay of the Caspian Sea and drilling of the area must be carried out from bulk islands. The construction of such islands, and they, due to technical requirements, have dimensions of 200x200 meters and a height of more than 3 meters, is very laborious and costly, even in the presence of highly productive construction equipment [5]. It becomes obvious that it is necessary to change approaches to the methods of additional exploration of the field. One of the ways to solve this problem may be the drilling of advanced exploratory directional shafts from existing wells under the bottom of the Balkan Gulf with displacements of 1000-1500 meters. This will avoid possible unjustified costs for drilling additional wells when delineating the deposit.
References:
- Деряев А.Р., Еседулаев Р. Основы технологии бурения при освоении нефтегазовых пластов методом ОРЭ. Научная монография. Ашгабат: Ылым. 2017. Стр 1-239.
- Деряев А.Р., Гулатаров Х., Еседулаев Р., Аманов М. Технология бурения наклонно-направленных горизонтальных скважин и расчеты по их проектированию / (монография) Ашгабат: Ылым. 2020. Стр 608
- Деряев А.Р. Разработка конструкции скважин для метода одновременно-раздельной эксплуатации нескольких нефтяных пластов. «Наука и техника в Туркменистане». №6. 2013. Стр 71-77.
- Деряев А.Р., Оразклычев Г., Еседулаев Р. Современное состояние изученности бурения направленных и многозабойных скважин с одновременно-раздельной эксплуатацией нескольких горизонтов (зарубежный опыт), Сборник статей Института нефти и газа, Выпуск 8. Ашхабад: Туркменская Государственная издательская служба, 2014. Стр 228–237
- Деряев А.Р. Особенности технологии бурения для одновременно-раздельной эксплуатации нескольких горизонтов на испытанных скважинах месторождения Северный Готурдепе, Сборник статей Института нефти и газа, Выпуск 8. Ашхабад: Туркменская Государственная издательская служба, 2014. Стр 238–248.