Проектирование пресс-форм с привлечением системы моделирования процесса литья пластмасс Сoretech system Moldex3D
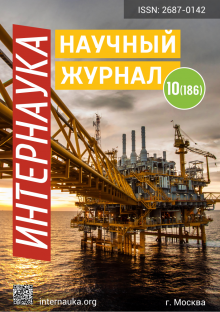
ПРОЕКТИРОВАНИЕ ПРЕСС-ФОРМ С ПРИВЛЕЧЕНИЕМ СИСТЕМЫ МОДЕЛИРОВАНИЯ ПРОЦЕССА ЛИТЬЯ ПЛАСТМАСС CORETECH SYSTEM MOLDEX3D
Перфилова Валерия Юрьевна
инженер – конструктор 3 категории, АО «НПК «КБМ»
РФ, г. Коломна
Абрамов Андрей Андреевич
инженер – конструктор 2 категории АО «НПК «КБМ»,
РФ, г. Коломна
Щебланов Виктор Анатольевич
инженер – технолог 1 категории АО «НПК «КБМ»,
РФ, г. Коломна
Миронов Юрий Александрович
инженер – конструктор 1 категории АО «НПК «КБМ»,
РФ, г. Коломна
Попов Андрей Александрович
инженер – технолог 2 категории АО «НПК «КБМ»,
РФ, г. Коломна
Синицын Дмитрий Александрович
начальник технологического отдела АО «НПК «КБМ»,
РФ, г. Коломна
DESIGN OF MOLDS WITH THE INVOLVEMENT OF THE SYSTEM FOR SIMULATION OF THE PLASTIC CASTING PROCESS CORETECH SYSTEM MOLDEX3D
Valeria Perfilova
Engineer - designer of the 3nd category joint stock company research and production corporation “KBM”,
Russia, Kolomna
Andrey Abramov
Engineer - designer of the 2nd category joint stock company research and production corporation “KBM”,
Russia, Kolomna
Viktor Shcheblanov
Engineer - technologist of the 1st category joint stock company research and production corporation “KBM”,
Russia, Kolomna
Yuri Mironov
Engineer - designer of the 1st category joint stock company research and production corporation “KBM”,
Russia, Kolomna
Andrey Popov
Engineer - technologist of the 2nd category joint stock company research and production corporation “KBM”,
Russia, Kolomna
Dmitry Sinitsyn
Head of the technological department joint stock company research and production corporation “KBM”,
Russia, Kolomna
АННОТАЦИЯ
В выпускаемых изделиях содержится определенная номенклатура деталей и сборочных единиц из термо- и реактопластов, получаемых из пресс-форм методом литья под давлением. В связи с переходом предприятий на серийный выпуск изделий выдвигаются и новые требования к проектированию и изготовлению пресс-форм.
ABSTRACT
The manufactured products contain a certain range of parts and assembly units from thermo- and thermosetting plastics obtained from molds by injection molding. In connection with the transition of enterprises to serial production of products, new requirements are also put forward for the design and manufacture of molds.
Ключевые слова: проектирование пресс-форм, PTC Creo 6.0, Moldex3D, симуляция.
Keywords: mold design, PTC Creo 6.0, Moldex3D, simulation.
Так как современное производство уже не может обходиться без автоматизации и использования современных программных продуктов, то и проектирование пресс-форм проводится с применением новейших программных средств таких как PTC Creo 6.0 (Рис.1) и Coretech system Moldex3D. Что позволяет значительно сэкономить время и свести к минимуму наличие конструкторских ошибок.
Рисунок 1. Применение Creo 6.0 в проектировании пресс-форм
Рассмотрим пример использования возможностей Creo 6.0 для создания литьевой формы для детали Обтекатель.
Данная деталь имеет сложную геометрическую поверхность, которая должна полностью формироваться в полости пресс-формы без дополнительной механической доработки (Рис.2).
Рисунок 2. 3D-модель детали Обтекатель
На первом этапе проектирования на основе конструкторской модели создается ссылочная модель, содержащая в себе доработки с учетом технологических требований такие как: припуски, литейные радиусы, формовочные уклоны. Здесь же закладываются и данные об усадке материала детали.
Следующим этапом является проектирование формообразующих элементов таких как пуансон (Рис.3) и матрица (Рис.4). Они получаются путём "отпечатка" отливки (ссылочной модели) на матрице/пуансоне которые в свою очередь становятся элементами формообразующего блока. Следующим шагом создается плоскость разъема пресс-формы, и далее система автоматически определяет конфигурацию матрицы и пуансона и сохраняет их в виде отдельных деталей, имеющих одну сборку.
а) б)
Рисунок 3. Пуансон пресс-формы: а) 3D-модель б) готовая деталь
Третьим этапом проектирования становиться добавление унифицированных элементов конструкции таких как: плиты крепления, колонки, втулки, направляющие выталкивающего механизма и т.д. Из библиотек программы добавляются детали крепежа и другие необходимые по ГОСТу детали, и сборки.
а) б)
Рисунок 4. Матрица пресс-формы: а) 3D-модель б) готовая деталь
На конечном этапе инженер-конструктор получает корректную 3D - модель сборки пресс-формы (Рис.5). Так же, с помощь возможностей Creo 6.0 можно еще на этапе проектирования проверить работу пресс-формы, а именно: раскрытие пресс-формы, работу механизма выталкивания и извлечения отливки. Благодаря применению Creo 6.0 в проектировании пресс-форм вероятность конструкторской ошибки даже у молодого специалиста сводится к минимуму.
Рисунок 5. 3D - модель сборки пресс-формы
Далее на основе спроектированных 3D-моделей автоматически создается графика чертежей сборки пресс-формы (Рис.6) и ее составляющих деталей. Все модели деталей и чертежи имеют ассоциативную связь, и при изменении параметров модели, размеры на чертеже меняются автоматически. Следовательно, если конструктор внесет изменения размеров в свою модель детали, то модель сборки пресс-формы и все формообразующие детали автоматически перестроятся. Все данные изменения автоматически распространятся на зависимую конструкторскую документацию.
Рисунок 6. Сборочный чертеж пресс-формы
Система моделирования процесса литья Coretech system Moldex3D
Технология литья под давлением для инженера – конструктора требует понимания многих процессов, происходящих в пресс-форме. Впрыск расплавленного материала с определенной температурой и под определенным давлением, и в итоге получение качественной детали определяют круг профессиональных знаний инженера-конструктора. Раньше можно было опираться только на накопленные знания, полученные экспериментальным путем предыдущих поколений. Теперь мы можем использовать системы моделирования процессов заполнения пресс-форм материалом под давлением (Рис.7). Данный метод позволяет прогнозировать поведение процесса литья и дает возможность снижения потребности в опытных образцах, позволяет устранить потенциальные производственные дефекты отлитых деталей еще на стадии проектирования пресс-форм.
Рисунок 7. Coretech system Moldex3D
Моделирование процесса литья под давлением дает возможность проанализировать равномерность заполнения полости литьевой пресс-формы, что позволяет увидеть места недоливов, пузырей и мест нахождения линий спая. Цветовая диаграмма показывает контурные цвета, которые представляют поток материала в литейной полости. В результате, темно-синим показаны места, которые заполняются в начале впрыска, а красным цветом, участки, заполняемые последними. Участки, которые не заполняются материалом не имеют цвета. В данном случае деталь полностью проливается и не имеет таких зон.
Рисунок 8. Цветовая диаграмма заполнения полости пресс-формы
Там, где встречаются два фронта потока материла, образуются линии спая (Рис.9). Результат расчета отображает угол конвергенции в градусах. Линии спая могут вызвать структурные проблемы и сделать участок визуально дефективным. При такой конструкции проблемные места неизбежны, так как передний фронт потока двух направлений объединяется вокруг отверстия, как в нашем случае. (или, если отливка-деталь имеет несколько литников). В данной детали линии спая находятся на некритичном участке, поэтому это не является проблемой.
Рисунок 9. Места нахождения линий спая
Воздушные ловушки возникают там, где поток расплава сжимает пузырек воздуха или газа между двумя направлениями сходящегося потока, или между фронтом потока и стенкой полости (Рис.10). Как правило, результатом является небольшое отверстие или пятно на поверхности детали. Результат расчета показывает, насколько серьезны воздушные ловушки и где они скорее всего будут. Воздушные ловушки могут быть приемлемыми, если они возникают на поверхности, которая не должна быть визуально идеальной, как в нашем случае.
Знание направленности волокон является полезным для оценки механических свойств детали (Рис 11). Например, ударная вязкость обычно значительно выше в направлении ориентации волокон в детали. При использовании волоконно-наполненных полимеров, предел прочности на разрыв также выше в направлении ориентации волокон. Рассматриваемая деталь, в последствии, будет проходить виброиспытания по поверхности, вдоль которой сориентированы волокна, что дает залог прочности.
Рисунок 10. Места нахождения воздушных ловушек
Управление ориентацией волокон пластмассы помогает предсказать направление линейной усадки и коробление литой детали.
Рисунок 11. Ориентация волокон волоконно-наполненного полимера
На данный момент спроектированная пресс-форма изготовлена инструментальным цехом и введена в эксплуатацию (Рис.12). Испытание проходило на участке гидравлических прессов цеха 2.
Рисунок 12. Пресс-форма для литья детали «Обтекатель»
В результате, применение новейших программных средств в проектировании и анализ полученных данных после привлечения системы моделирования процесса литья пластмасс Coretech system Moldex3D позволяет:
1. Сократить время на проектирование оснастки
2. Быстро передать навыки проектирования молодому специалисту
3. Свести к минимуму конструкторские ошибки
4. Уменьшить время внедрения оснастки в производство
5. Снизить потребности в опытных образцах
6. Устранить потенциальные производственные дефекты отлитых деталей еще на стадии проектирования пресс-форм.
7. Снизить стоимость изготовления оснастки
Список литературы:
- Басов Н. И., Брагинский В. А., Казанков Ю. В. Расчет и конструирование формующего инструмента для изготовления изделий из полимерных материалов // Учебник для вузов. – М.: Химия, 1991. – 352 с. (дата обращения: 26.07.2020).