RESEARCH OF OXYCLOURIDE OF COPPER POWDER BY AMONIAC
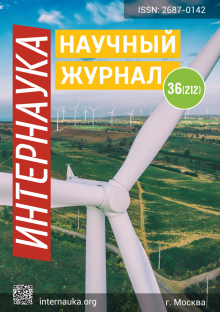
RESEARCH OF OXYCLOURIDE OF COPPER POWDER BY AMONIAC
Ngo Huy Khoa*
Ph.D, Institute of Materials Science – Vietnam Academy of Science and Technology,
Vietnam, Hanoi
Nguyen Thi Hong Nhung
M.S., Sao Do University - Ministry of Industry and Trad,
Vietnam, HaiDuong
Vu Hoa Ky
Ph.D, Sao Do University - Ministry of Industry and Trad,
Vietnam, HaiDuong
Acknowledgment: This research was supported by a pilot production project under the National Science and Technology program, with the code CNKK.013.19, to serve the renewal and modernization of mining and mineral processing technology by 2025.
ABSTRACT
The paper describes the process of producing copper oxychloride from copper powder. Pure chemicals such as NH3, H2O2, NH4Cl, and H2SO4 are used as input materials. According to the results, the optimal mixing ratio for 100g of copper powder was as follows: 12 g of NH3, 60-80 g of H2O, 28 g of H2O2, and 170 g of NH4Cl. After 20 days, analysis of the phase composition of this mixed powder sample indicated that Atacamide (Cu2Cl(OH)3) accounted for the majority of the content, ranging from 90.2 to 92.5 %. Furthermore, after 25 days, the conversion efficiency of copper oxychloride to copper sulphate in 200l H2SO4 5M is 93.0 – 95.0 %..
Keyword: Oxychloride, copper powder, conversion efficiency.
1. INTRODUCTION
Copper and its compounds have been used in a wide range of applications, including:
- Copper sulfate is a fungicide, bactericide, electroplating agent, and forage additive.
- As a corrosion-resistant material, an alloy of copper and iron/nickel is used, such as sliding silver.
- A copper-phosphorus alloy used to make copper pipes with high heat resistance, high pressure resistance, and ductility..
- Copper oxide is used as a pigment in paints, ceramics, and other products.
This research report will present a novel method for converting copper powder to copper oxychloride via ammonium hydroxide and catalysis. Copper oxychloride has a wide range of applications, including fungicides, mold inhibitors, and as an intermediate in the production of copper oxide and copper sulfate.
2. MATERIALS AND METHODS
2.1. Materials and equipments
In following ASTM standards, pure red copper powder has a maximum particle size of 500 m and is grade C11000. Table 1 shows the contaminant composition.
The stainless steel mixer has a capacity of 10 l and is equiped with a gas treatment system before being discharged into the outside environment
At 90 rpm, the reaction was stirred. The ph was determined using a MILWAUKEE MW-101 handheld pH meter.
Pure reagents such as NaCl, ammonia, and sulfuric acid are used.
Table 1.
Chemical composition of copper powder
Element |
Cu |
P |
Bi |
Sb |
As |
Fe |
Ni |
Pb |
Sn |
S |
Zn |
O |
Others |
Ingredient (% mas.) |
99.95 |
0.001 |
0.001 |
0.002 |
0.002 |
0.005 |
0.002 |
0.003 |
0.002 |
0.005 |
0.005 |
0.02 |
0.005 |
2.2. Methods of research and analysis
The following experimental steps are carried out in the following order:
- Step 1: Each test set was mixed with a fixed 100 g of copper powder, ammonium hydroxide, NH4Cl, and H2O2 in a predetermined ratio.
The following basic reactions can occur during the process of converting copper powder to oxychloride [1-3].
Cu + H2O2 + 4NH3 = [Cu(NH3)4](OH)2 |
(1) |
4Cu+8NH3+2H2O+O2 = 4[Cu(NH3)2]++4OH- |
(2) |
[Cu(NH3)2]+ + NH4Cl = CuCl + NH4+ + 2NH3 |
(3) |
[Cu(NH3)4](OH)2 + 2NH4Cl = Cu(NH3)4Cl2 + 2NH4OH + |
(4) |
2Cu+4NH4Cl + O2 + 2H2O = 2CuCl+4NH4OH+Cl2 |
(5) |
2Cu(NH3)4Cl2 + 6Cu + 3O2 + 6H2O ® 4Cu2Cl(OH)3 + 8NH3 |
(6) |
4CuCl + 4Cu + 3O2 + 6H2O ® 4Cu2Cl(OH)3 |
(7) |
In general, all of the reactions listed above can occur in the atmosphere. For reactions (1,2), equilibrium is reached quickly. NH3 acts as a catalyst to make Cu ions more mobile, allowing reactions (1-5) to proceed more quickly.
- Step 2: Apply the mixture thinly to the floor and leave it there for 20-30 days.
- Step 3: Dissolve the mixture in sulfuric acid while keeping the pH constant at 4. The reaction time is 10 minutes. The amount of 5M H2SO4 solution used was 200 l.
CuSO4 is obtained according to the following reaction:
(8)
- Step 4: Set the solution aside for 3 hours to settle. Copper content in solution was determined using an ICP MS instrument at the Institute of Chemical Technology of the Vietnam Academy of Science and Technology. As a result, the solubility of copper is calculated according to the following formula:
H (%) (9)
Where: MCu - copper ion concentration (g/l)
H- the copper oxychloride conversion efficiency (%).
3. RESULTS AND DISCUSSION
3.1. Effect of the amount of NH3
The amount of Cu used was set at 100g. According to the reaction equations (1-7), the amount of NH3 is changed from 2 to 20% compared to the theory, corresponding to 2g to 20g NH3. Table 2 shows the chemical content of each reaction set.
Table 2.
Substance mixing ratios for a batch of reactions
Set |
1st |
2nd |
3rd |
4th |
5th |
Cu (g) |
100 |
100 |
100 |
100 |
100 |
H2O2 (g) |
28 |
28 |
28 |
28 |
28 |
NH4Cl (g) |
170 |
170 |
170 |
170 |
170 |
NH3 (g) |
4 |
8 |
12 |
16 |
20 |
H2O (g) |
60 |
60 |
60 |
60 |
60 |
The results of copper ion concentration analysis and copper conversion efficiency are shown in Table 3.
Table 3.
Concentration of copper ions in solution after reaction and conversion efficiency
Set |
1st |
2nd |
3rd |
4th |
5th |
MCu (g/l) |
10.56 |
42.67 |
46.70 |
45.80 |
45.40 |
H (%) |
21.12 |
85.34 |
93.40 |
91.60 |
90.80 |
Figure 1. The dependence of the soluble copper content and the copper oxychloride conversion efficiency on the amount of NH3
The optimal mix ratio, as shown in Figure 1, is 12 g NH3/100 g Cu. The conversion rate of copper to copper oxychloride was up to 93,4 % at the time.
In addition, after the 2nd step the samples after mixing according to the ratio in Table 3 are analyzed for phase composition. Table 4 shows the result of the phase composition analysis.
Table 4.
Mineral composition of powder samples after 20 days (after 2nd step)
Phase composition |
Content (% Mas.) |
||||
M1 |
M2 |
M3 |
M4 |
M5 |
|
Atacamit- Cu2Cl(OH)3 |
6.8-7.4 |
80.3-83.4 |
90.2-92.5 |
88.6-90.2 |
85.3-87.6 |
Cuprum- Cu |
32.6-34.2 |
4.2-5.1 |
2.7-3.3 |
1.4-2.5 |
2.1 -3.8 |
Amoni clorua -NH4Cl |
55.2-58.6 |
8.2-9.4 |
1.2-5.1 |
3.0-5.0 |
4.1-6.4 |
Coesit – SiO2 |
1.3-3.4 |
1.3-2.8 |
1.2-3.1 |
1.4-3.8 |
1.6-3.1 |
Lepidocrocit+Gơtit (Fe2O3.H2O) |
0.1-1.2 |
0.1-1.2 |
0.1-1.2 |
0.1-1.2 |
0.1-1.2 |
Cupro chloride |
6.1-8.7 |
1.3-3.4 |
0.1-0.3 |
1.2-2.8 |
0.8-1.3 |
According to Table 4, the atacamide content in sample M3 is the highest, ranging from 90.2 to 92.5 %.
The optimal amount of NH3 for 100g Cu is 12 g.
3.2. Effect of the amount of water added
The varieties contain 20, 40, 60, 80, 100, and 120 g of water, respectively. The mass of NH4Cl was established at 170 g. Table 3 shows the substance content of each sample:
Table 5.
Substance mixing ratios for a set of reactions
Set |
1st |
2nd |
3rd |
4th |
5th |
6th |
Cu (g) |
100 |
100 |
100 |
100 |
100 |
100 |
H2O2 (g) |
28 |
28 |
28 |
28 |
28 |
28 |
NH4Cl (g) |
170 |
170 |
170 |
170 |
170 |
170 |
NH3 (g) |
12 |
12 |
12 |
12 |
12 |
12 |
H2O (g) |
20 |
40 |
60 |
80 |
100 |
120 |
Table 6.
Concentration of copper ions in solution after reaction and conversion efficiency
Set |
1st |
2nd |
3rd |
4th |
5th |
6th |
H2O, (g) |
20 |
40 |
60 |
80 |
100 |
120 |
MCu , (g/l) |
6.7 |
36.5 |
46.7 |
45.8 |
40.5 |
20.7 |
H, (%) |
13.40 |
7.00 |
93.40 |
91.60 |
81.00 |
41.40 |
Figure 2. The dependence of the soluble copper content and the copper oxychloride conversion efficiency on the amount of H2O
The copper conversion reaction occurred unfavorably with an efficiency of less than 85 % when the amount of water involved in the reaction was improved from 20 to 50 g. When a large amount of water, ranging from 90 to 120 g, is added, the penetration of atmospheric oxygen into the reaction zone is affected, and the amount of dissolved oxygen is insufficient, resulting in an incomplete reaction.
As a result, the optimal amount of water to react with 100g of copper is 60-80 g.
3.3. Effect of reaction time and copper particle size
The researched size region was divided into regions up to 500 µm (Table 7) to investigate the effect of copper particle size on dissolution efficiency. The experiment was conducted at the following fixed parameters: 100 g of copper powder, 28 g of H2O2, 170 g of NH4Cl, 12 g of NH3, and 70 g of H2O.
Table 7.
Effect of copper particle size on the conversion efficiency to oxychloride
|
Size, µm |
Reaction time, (day) |
||||
5 |
10 |
15 |
20 |
25 |
||
H, (%) |
≤100 |
6.7 |
36.5 |
46.7 |
93.4 |
95.4 |
100-200 |
5.7 |
30.5 |
36.7 |
93.6 |
93.4 |
|
200-300 |
4.7 |
26.5 |
26.7 |
91.4 |
92.4 |
|
300-400 |
3.7 |
16.5 |
16.7 |
90.8 |
93.8 |
|
400-500 |
2.7 |
6.5 |
9.7 |
90.6 |
93.1 |
Figure 3. Effect of reaction time and copper particle size on conversion efficiency
Figure 3 shows that in order for the reaction to occur completely with all of the particle size regions researched, the reaction time must be around 20-25 days, with a maximum conversion efficiency of 93.0 – 95.0 %. As a result, the chosen reaction time is 23 - 25 days.
4. CONCLUDE
NH3 serves as a catalyst, accelerating the process of converting copper powder to copper oxychloride form.
For 100g of copper powder, the optimal mixing ratio was 12 g NH3, 60-80 g H2O, 28 g H2O2, and 170 g NH4Cl. After 20 days, the majority of the Atacamide phase is present in this mixed powder sample, with levels ranging from 90.2 to 92.5 %.
After 25 days, the conversion efficiency of copper oxychloride to copper sulphate in 200l H2SO4 5M is 93.0 -95.0 %.
References:
- Kể chuyện kim loại – X.I.Venetxki – Nhà xuất bản khoa học Khoa học kỹ thuật.
- Gold cementation from Ammonium Thiosulfate solution bay Zinc, Copper and Aluminium Powders – Harunobu Arima, Toyohisa Fujita, Wan-Tai Yen – 201
- Dissolution of Copper in Chloride/Ammonia Mixtures and the Implications for the Stress Corrosion Cracking of Copper Containers - F. King, G. Greidanus, DJ. Jobe- Whiteshell Laboratories Pinawa, Manitoba, Canada ROE 1L0 - 1999.
- Nghiên cứu khả năng điều chế atacamite từ tinh quặng sunfua đồng sau thiêu - Phạm Đức Thắng , Ngô huy Khoa , Nguyễn Trung Kiên.