RESTORING WELL PRODUCTIVITY BY ACID TREATMENT AND EXPOSURE TO PNEUMATIC EXPLOSION
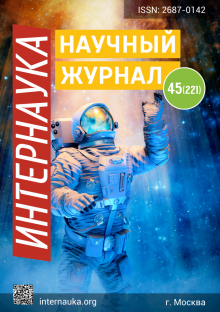
RESTORING WELL PRODUCTIVITY BY ACID TREATMENT AND EXPOSURE TO PNEUMATIC EXPLOSION
Shuxrat Aliqulov
Doctor of technical sciences, chairman of department, Navoi State Mining Institute,
Uzbekistan, Navoi
Sukhrob Khamidov
Assistant, Navoi State Mining Institute,
Uzbekistan, Navoi
Dilfuza Mansurova
Student, Navoi State Mining Institute,
Uzbekistan, Navoi
Ozoda Odilova
Student, Navoi State Mining Institute,
Uzbekistan, Navoi
ABSTRACT
Treatment of the bottomhole formation zone of wells, as well as increasing their productivity and permeability using acid and impulse treatment technology, which is one of the most effective methods of increasing production rates in wells, is designed to clean and restore filtration properties and stimulate fluid flow.
Keywords: well, in-situ leaching, acid, hydro-flow bottomhole, extract, impulse, hydrostatic, filter zone.
With the content of carbonate-containing rocks in the productive horizon, an additional stage of well development is acid treatment of the near-filtration zone of the well [1].
The main acid used is HCl and a few others. It effectively acts on calcium or magnesium carbonate to form a soluble and easily removable chloride compound.
Other acids are also used: nitric, hydrofluoric, etc.
When an acid solution is injected into the formation, the pores in the bottomhole formation zone are cleaned and expanded. Thus, restoring the impaired permeability of the treated zone, and in some cases even increasing its initial value.
With uniform penetration of the acid solution into the voids of the productive formation around the well, the radius of the zone of penetration of unreacted acid is determined from the expression [2]:
where, q – is the volume of the acid solution;
t – is the duration of the reactions until the acid solution is neutralized;
h – is the thickness of the formation;
m – is the porosity of the rock;
rc – borehole radius.
The technology of work is as follows: the openness of the well filter is checked, if necessary, it is cleaned of sand and suspended matter.
Preparation of solutions for chemical treatment and well treatment. Due to the absence of gummed containers for diluting acid solutions, the solution is prepared according to the following scheme.
Open the supply of the working solution to the well being treated, adjust the supply of solutions to 1 m3/h, open the supply of acid at a flow rate of 1 m3/h. The total flow rate will be 2,0 m3/h, the fluid is displaced in the well, the concentration of the acidic solution will be in the range of 12-15%, the solution will be fed for 45 minutes, the volume of the supplied solution will be 1,5-2,0 m3. If the volume of the solution in the well is more than 1,5 m3, increase the time for supplying the solution.
The wellbore and the bottomhole zone of the filter should be processed during self-pouring (displacement of solutions in the receiving funnel).
Extract the acid in the wellbore for 16 hours.
After acid treatment, the wells are intensively pumped with an Atlas-Copco compressor, the hose is lowered under the solution level to the maximum possible depth. The solutions are discharged into an evacuation manifold.
The quality of the technical hydrochloric acid used must comply with the normative characteristics, especially with regard to the content of impurities.
Recovery of well productivity by means of pneumatic explosion.
The mechanism of pneumatic explosive action in a well is as follows.
The compressed air previously accumulated in the chamber is exhausted into the liquid at high speed and expands, forming an air bubble. A sharp compression of the adjacent layers of a liquid lead to the propagation of an acoustic compression wave in it and a simultaneous radially diverging motion of the hydraulic flow [3].
As long as the pressure in the bubble is greater than in the environment, the hydro-flow moves with some acceleration. The mass of liquid, having received a certain impulse, from the moment when the pressure in the bubble is equalized with the hydrostatic pressure in the well, moves by inertia and, in turn, acts on the bubble, causing its expansion. The cavity pressure continues to drop and eventually becomes less hydrostatic.
As a result, the bubble collapses, then pulsates and floats. These processes are accompanied by energy exchange, which manifests itself in the form of work performed due to the loss of the internal energy of the air bubble.
The energy accumulated in the pneumatic unit is assessed according to the dependence:
where, Рн and Vн – initial pressure and volume of compressed air in the working chamber; Ка – is the adiabatic exponent.
The residual energy of the air bubble at the end of its expansion is, respectively, equal to:
where, Рmin and Vmax – are the final pressure and volume of the air bubble.
In accordance with this, the work performed during the pneumatic explosion is determined by the difference between the accumulated and residual energy and the work expended to overcome the hydrostatic pressure hгс, which is estimated by the formula:
where, Ро – hydrostatic pressure.
In the cramped conditions of the well, when the bubble expands, the reaction forces of rigid boundaries act on it.
The predominant radially diverging movement of compressed air in the initial period of bubble formation under the influence of liquid backpressure is easily deformed, pulling the air cavity towards more mobile boundaries. This causes a redistribution of the energy of the bubble and its concentration on the weakest points. As a result, the bubble lengthens along the axis of the well, but in certain cases (for example, with uneven clogging of the filter and the filter zone or the adhesion of the pneumatic gun to the filter wall), compressed air can penetrate into the filter zone [1].
The treatment of wells by pneumatic explosion is carried out according to a special technological map, where, along with the necessary characteristics of the well and the filter, the sequence and parameters of all the main, preparatory, final and auxiliary operations, the used technological and auxiliary equipment, tools and instrumentation are indicated. Technological control over the course of pneumatic explosive treatments is carried out by assessing the volume of sludge accumulated in the sludge collector under the pneumatic nozzle and the degree of siltation of the sump and filter. Correspondence of cuttings volume calculated according to the degree of saturation of rocks near the filter zone is an indicator of complete decolmatation of the well.
References:
- КОМПЛЕКСЫ ПОДЗЕМНОГО ВЫЩЕЛАЧИВАНИЯ - А.А. Кедровский – издательство Недра, Москва, 1991.
- ПРОЕКТИРОВАНИЕ ПРЕДПРИЯТИЙ ПО ДОБЫЧЕ И ПЕРЕРАБОТКЕ РУД РЕДКИХ И РАДИОАКТИВНЫХ МЕТАЛЛОВ – И.У. Халимов, С.Б. Хамидов, Н.М. Каримов –Учебно-методическое пособие для выполнения практических работ. Издательство НГГИ, Навои, 2020)
- БУРЕНИЕ ГЕОТЕХНОЛОГИЧЕСКИХ СКВАЖИН БЕЗГЛИНИСТЫМИ РАСТВОРАМИ: ТЕХНИЧЕСКОЙ ВОДОЙ И АЭРИРОВАННЫМ ПАВ РАСТВОРОМ – А.С. Йулдашев, Б.Д. Шаропов, Н.М. Каримов, И.У. Халимов – Москва, CLXV-ая международная научно-практическая конференция «Молодой исследователь: вызовы и перспективы», 2020.