STUDY ON THE PROCESS OF SEPARATING NICKEL FROM NICKEL STENCIL BY DIRECT VAPORIZATION IN A GRAPHITE FURNACE AT ATMOSPHERIC PRESSURE
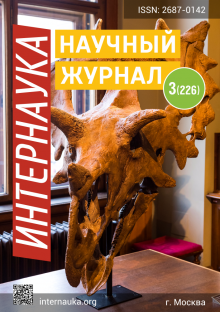
STUDY ON THE PROCESS OF SEPARATING NICKEL FROM NICKEL STENCIL BY DIRECT VAPORIZATION IN A GRAPHITE FURNACE AT ATMOSPHERIC PRESSURE
Do Nguyen Huy Tuan
M.S., Institute of Materials Science – Vietnam Academy of Science and Technology,
Vietnam, Hanoi
Pham Duc Thang
Assoc. Prof., Ph.D, Institute of Materials Science – Vietnam Academy of Science and Technology,
Vietnam, Hanoi
Nguyen Trung Kien
M.S., Institute of Materials Science – Vietnam Academy of Science and Technology,
Vietnam, Hanoi
Ngo Huy Khoa
Ph.D, Institute of Materials Science – Vietnam Academy of Science and Technology,
Vietnam, Hanoi
Nguyen Ba Phuong
M.S., Institute of Materials Science – Vietnam Academy of Science and Technology,
Vietnam, Hanoi
Dao Van Kien
M.S., Sao Do University - Ministry of Industry and Trad,
Vietnam, HaiDuong
Nguyen Thi Lieu
M.S., Sao Do University - Ministry of Industry and Trad,
Vietnam, HaiDuong
Acknowledgment: This study was financed by the Science and Technology Project under the Vietnam Academy of Science and Technology's priority Science and Technology directions: "Research on producing nickel from high-quality nickel sten in a CO-rich atmosphere at normal pressure", Code: VAST03.03/19-20.
ABSTRACT
Carbonylation is one of the primary methods for refining nickel once it has been recovered from primary ores. This method is currently used in the world in conditions of temperature 220-2500C and high pressure 220-230 atm, requiring expensive equipment investment and a complicated operation process. The authors of the Institute of Materials Science of the Vietnam Academy of Science and Technology developed a research carbonylation method in a simple induction furnace device at normal air pressure, allowing for the speedy separation of nickel directly from nickel sulfide in the form of sten powder. This paper describes the experiments and results obtained the metal nickel powder with size 10-20 µm, purity over 99.5 percent, and rate recovery is 95%.
Keyword: carbonylation, nickel powder, vaporization, graphite furnace.
I- INTRODUCTION
The carbonylation method is generally used to produce of nickel from ores in the area of nickel metallurgy. The carbonylation method is based on the following reaction.
Ni + 4CO « Ni(CO)4 + 40.000 cal (1)
Prior to World War II, the above method was used in England [1,2]. However, for the reaction to occur at atmospheric pressure, the source of CO must always be fresh and for an extended period of time (up to 8 months per cycle). As a result, working equipment became extremely cumbersome and complex, requiring a lot of energy and being inefficient.
From World War II to the present, the carbonylation process has been completed and changed when the reaction (1) is carried out under the following conditions: The CO pressure can reach 200-230 atm, and the reaction temperature can range between 2200C and 2500C.
At high temperatures and pressures, reaction 1 continues to occur intensely from left to right, reducing the overall pressure of the system [1-3]. However, at such high temperatures, Fe and Co react with CO to produce pentacarbonyl iron - Fe(CO)5 and tetracarbonyl cobalt - Co2(CO)8. Further condensation and separation of the Cabonyl fumes of Fe and Co are required to obtain nickel tetracarbonyl. As a result, this technique does not provide a high level of economic efficiency.
There have been various studies on the thermodynamics of process (1) at high temperature and pressure [3-6], but almost none of them have indicated the possibility of over-strengthening Nickel vaporization with high efficiency at atmospheric pressure.
A research team from the Vietnam Academy of Science and Technology's Institute of Materials Science has completed direct separation of nickel from nickel sten in a graphite furnace. The concept is to use the CO produced by the anaerobic burning of graphite in the following reaction:
C + O2 = CO2 (2)
C + CO2 = CO (3)
According to the reaction (1) , the CO gas created directly in the furnace will effectively combine with the nickel in the sten. The process produces tetracarbonyl nickel - Ni(CO)4 in vapor form. This vapor will be sent into the pyrolysis chamber, where it will be converted into nickel metal powder.
II- EXPERIMENT
1- Equipment
Figure 1 shows research apparatus for separating nickel by vaporization.
Figure 1. Experimental apparatus for direct nickel separation from nickel sten
1. High frequency induction electric furnace 1600w; 2. Graphite Furnace; 3. Tetracarbonyl vapor and residual pipe line; 4. Pyrolysis chamber produces nickel powder; 5. Exhaust fan; 6. Electrical cabinet.
2- Induction graphite furnace.
Working capacity of graphite furnace is 200ml.
Figure 2. Actual graphite furnace image
3- Materials
The nickel stencils were produced from nickel concentrates using the method described in the publication [7]. Table 1 shows the chemical element content of nickel stencil powder.
Table 1.
Content of main chemical elements in sten powder
Elements |
Ni |
Cu |
Fe |
S |
W, % |
20-25 |
9-12 |
40-42 |
18-22 |
Table 2.
EDX spectrum and chemical composition of nickel stencil powder
|
|
4- Analytical equipment and methods
- The built-in temperature sensor refers to the temperature in the oven.
- The handheld device is used to measure CO emissions from graphite furnaces (Figure 3).
- Analytical Methods: ICP-MS, SEM-EDX.
Figure 3. CO . measuring device
5) Experimental procedure
a) Preparation of ingredients:
- Grinding the input material (nickel stencil) to a particle size of less than 100 mm to ensure thorough conversion.
- The graphite is powdered to a particle size of 50-200 mm .
- SiO2 is grinded to a particle size of 50-75 mm.
- Mixing ingredients
- The sten powder is mixed with graphite powder and SiO2 powder in a mass ratio of 1: 0.3: 0.1.
- In an anaerobic environment, graphite powder reacts to produce CO. The porous SiO2 powder will allow CO gas to easily enter the furnace, creating a reaction with the sulfide powder to form nickel tetracarbonyl gas, which may easily escape to the top.
- Inputting the component mixture into the graphite furnace
In the oven, the height of the dough mixture approaches a ratio of 0.5-0.8 times the height of the oven pot. When this ratio falls under 0.5, the reactor is unable to meet its design capacity. When the ratio exceeds 0.8, the upper material is easily removed by the created gas flow.
- Working operation of tetracarbonyl gas pyrolysis furnace
The working temperature of the furnace is maintained at 180-200°C.
- Equipment operation
After completing the preceding stages, turn on the magnetic induction furnace and heat it to a high temperature enough to carry out the nickel tetracarbonyl process. When the radial temperature reaches 150°C, the temperature sensor in the mixing chamber's center (centrifugal) will actively cut off the current, ensuring that no iron carbonyl Fe(CO)5 vapor is created at higher temperature than this.
The tetracarbonyl gas stream is transported to the pyrolysis furnace during the induction furnace operation. At a temperature of 180-200°C, the gas is transformed to metallic nickel powder. The vapor of nickel tetracarbonyl can be transported to the pyrolysis furnace by itself or by an exhaust fan.
When the magnetic induction furnace is turned off, switch off the pyrolysis furnace to recover the metallic nickel powder.
III- RESULTS AND DISCUSSIONS
1- CO production during the heating process
At various temperatures, the CO concentrations released from the furnace under idling and loaded kiln conditions were measured. Figure 4 and Table 3 show the experimental outcomes.
Table 3.
CO concentration in the induction graphite furnace
T, oC |
C(CO) idling kiln, ppm |
C(CO) loaded kiln, ppm |
200 |
249 |
10 |
300 |
297 |
9 |
400 |
345 |
8 |
Figure 4. The dependence of CO content on furnace temperature
The results showed that whenever the furnace was idle, the concentration of CO gas increased as the temperature increases. When compared to the no-load case, the CO content is decreased by 25-30% in the loaded condition. It demonstrates that a significant amount of CO (approximately 95-97 %) was lost during the nickel vaporization reaction in the sten to form tetracarbonyl nickel.
2- Nickel vaporization time in reactor
Conducted to identify the timing to turn off the furnace to end the vaporization process when the temperature in the furnace core reaches the limit of 1500C at the induction graphite furnace's operational temperature settings of 200-300-4000C. Table 4 and Figure 5 show the results.
Table 4.
Oven operating time at furnace center temperature 1500C
Temperature, 0C |
Operating time, h |
200 |
8.3 |
300 |
6.4 |
400 |
3.2 |
Figure 6. Dependence of the operating time on the temperature in the center of the furnace
The results demonstrate that when the furnace's working temperature increases, the vaporization process becomes stronger, and the time needed to complete the process decreases dramatically from 8.3h at 2000C to 3.2h at 4000C.
3- Efficiency of nickel recovery
To prevent the presence of Pentacarbonyl iron Fe(CO)5, the carbonylation process will be terminated when the mixture temperature reaches 150°C. As a result, the majority of the gas emitted is solid nickel carbonyl vapor. This gas is transformed into metallic nickel powder in the pyrolysis furnace. The product conversion rate was calculated based on the amount of nickel powder obtained.
Table 5.
EDX spectrum of sten powder residues after vaporization
|
The carbonylation process was investigated, and it was discovered that the nickel recovery efficiency was steady when the temperature at the center was regulated at a maximum of 150oC independent of the furnace operating temperature. However, in order for the pyrolysis process to completely convert the nickel carbnyl vapor, the pyrolysis furnace must have an acceptable working mode as well as a reasonable inlet and output airflow rate. Thus, the metal nickel recovery efficiency reached above 95% in 8.3 hours with the furnace operating mode set to 200oC.
4) Physical and chemical properties of recovered nickel powder
Metallic nickel powder pyrolysis from tetracarbonyl vapor has an uniform circular shape, with an average size of 10-15 µm, according to SEM pictures and EDX spectra (Figure 6). This size is five times higher than the average size of nickel powder produced in several Chinese and Russian factories [8].
- Analytical results showed that the nickel content reached over 99.5%. The product is not 100% pure due to small amounts of aluminum in the exhaust gas.
|
|
Figure 6. SEM image of metallic nickel powder
Table 6.
EDX spectrum and content of elements in nickel powder after pyrolysis
IV- CONCLUDE
- Direct nickel carbonylation from nickel stencil powder can be performed at high speed and normal pressure in an electric furnace equipped with a magnetic induction graphite furnace. The time required to complete the carbonylation process is determined by the heating level for the device's induction furnace, and the sensor controls the maximum temperature in the furnace core, ensuring the process is completed in the hourly unit of time.
- This process's nickel recovery rate can reach 95% and is independent of the direction of the induction furnace's heating rate.
- Pyrolysis nickel powder has an average particle size of 10-15 m, which is 5 times larger than the particle size of nickel powder produced by these powder manufacturers in China, the Russian Federation, and many other countries.
- Pyrolysis nickel powder with purity higher than 95%.
References:
- А.А.Цейдлер. Металлургия меди и никеля. Издателство Черной и Цветной Металлургии. Москва 1958.
- THERMODYNAMICS AND KINETICS OF THE CARBONYL PROCESS FOR THE REFINING OF NICKEL JITEN DAS, S.SRIKANTH and PREMCHAND Non-Ferrous Process Division National Metallurgical Laboratory, Jamshedpur 831 007, India. Proceedings of the International Conference on "Recent Advances in Metallurgical Processes" Golden Jubilee Celebrations, Department of Metallurgy, Indian Institute of Science, Bangalore Eds. D.H. Sastry, E.S. Dwarakadasa, G.N.K. lyengar and S. Subramanian New Age International Publishers, New-Delhi (1997).
- Kubaschewski 0., O.Knacke and K.Hesselman, "Thermochemical Properties of Inorganic Substances", 2nd ed., Springer Verlag, Dusseldorf, Germany, 1991
- Garner M.L. and D.Chandra, J. Phase Equil., 16 (1995) 24
- Swartzendruber L.K., V.P.Itkin and C.B.Alcock, J. Phase Equil., 12 (1991) 288
- Srikanth S. and Premchand, Report submitted to ISCP office of European Commission under Contract No CI1*-CT94-0055, February, 1997.
- Phạm Đức Thắng. Nghiên cứu luyện tinh quặng niken sulfua ra sten. TC Khoa học công nghệ Kim loại., vol 36, tr.35-40. ISSN 1859-4344. Hà nội 2011.
- Cabonyl metal powder production. 2017 International Conference on Powder Metallurgy & Particulate Materials. June 13-16, 2017 The Bellagio. Las Vegas